Explore extensive packaging machine repair service options in your region.
Why Timely Product Packaging Maker Repair Service Provider Are Important for Operational Effectiveness
In the competitive landscape of production, the function of timely packaging machine repair service solutions can not be overemphasized. Such services are necessary not only for reducing unplanned downtime yet additionally for cultivating a seamless manufacturing setting that satisfies client demands. By dealing with small breakdowns before they intensify, companies can considerably improve operational performance and decrease lasting prices. The implications of ignoring these services expand past instant repair services, increasing inquiries regarding equipment integrity and general productivity. What methods can business implement to ensure they remain proactive in their upkeep strategy?
Influence of Downtime on Production
Downtime in manufacturing can be compared to a ship adrift at sea; without a trusted training course, production procedures can quickly drift off track. The impact of downtime, especially in product packaging operations, can be both prompt and far-ranging.
Furthermore, unexpected downtime disrupts workflow, causing inadequacies that reverberate throughout the supply chain. Staff members might be left still, leading to reduced morale and productivity. Additionally, the price of emergency fixings typically goes beyond that of scheduled maintenance, additional straining funds.
In a competitive landscape, where time-to-market is crucial, the ability to keep consistent manufacturing levels ends up being critical. Downtime not just impacts prompt result yet can likewise develop a causal sequence that affects inventory levels, capital, and general operational efficiency - packaging machine repair service. Therefore, understanding and mitigating the impact of downtime is crucial for makers intending to maintain their competitive side and make sure long-lasting development
Advantages of Routine Maintenance
Regular maintenance of packaging devices works as a critical pillar in making certain undisturbed manufacturing and functional effectiveness. By executing a constant upkeep routine, services can dramatically enhance the dependability and longevity of their equipment. Regular assessments permit the prompt recognition of damage, preventing small concerns from escalating right into significant breakdowns.
Moreover, regular maintenance enhances maker performance, making certain that packaging processes operate at peak performance. This optimization not just enhances throughput however also lessens the possibility of product issues, thus maintaining high-grade criteria. Additionally, properly maintained devices add to power effectiveness, minimizing functional expenses connected with extreme power usage.
Along with performance advantages, normal upkeep promotes a much safer working environment. By ensuring that machines run properly, the danger of accidents and injuries created by tools failing is notably lowered. This dedication to safety and security not just protects workers however likewise aligns with governing compliance, alleviating prospective lawful liabilities.
Ultimately, investing in routine upkeep boosts general productivity, lowers unanticipated downtime, and promotes a society of aggressive possession administration. This tactical method guarantees that packaging procedures continue to be competitive in a busy market, which is essential for sustained success.
Cost Ramifications of Postponed Repair Services
Ignoring prompt repair services on product packaging machines can cause considerable economic consequences for companies. When equipment breakdowns, assembly line can halt, leading to lost output and delayed shipment schedules. packaging machine repair service. Each hour of downtime translates right into not only shed sales however likewise potential charges from customers due to unmet deadlines
Furthermore, postponed repair services can aggravate existing problems, resulting in much more extreme damage and boosted repair work expenses with time. A small malfunction might escalate right into a significant malfunction, necessitating expensive parts substitute or a full overhaul of the machine. This can stress budgets and divert funds from various other vital areas, hindering general operational development.
Additionally, services might encounter increased labor expenses as employees continue to be still or are reassigned during prolonged fixing durations. The longer equipment is out of solution, the more significant the influence on workforce performance.
Enhancing Tools Long Life

Implementing a routine upkeep routine can determine wear and tear early, avoiding tiny issues from escalating right into expensive failures. This positive technique not only boosts the machine's operational reliability yet likewise maximizes the general manufacturing workflow. Operators needs to additionally guarantee that machines are made use of according to maker requirements to prevent excessive stress and anxiety on essential parts.
Furthermore, spending in high quality substitute parts throughout fixings adds to equipment durability (packaging machine repair service). Utilizing ineffective elements might lead to constant breakdowns, negating any type of cost savings realized from more affordable repair work. Correct training for operators on finest techniques for device handling and procedure can also dramatically impact the equipment's life-span
Choosing the Right Repair Work Service
Choosing the proper repair work solution for product packaging machines is necessary for guaranteeing very little downtime and optimum performance. When assessing potential service companies, consider their industry experience and specialization in packaging go to this web-site machinery. A company with a tried and tested performance history in taking care of comparable equipment will likely possess the necessary experience to diagnose and solve problems effectively.
Additionally, assess the availability of service technicians and their action time to solution phone calls. A fixing service that provides 24/7 assistance can substantially lower the influence of unforeseen maker failures. Make inquiries regarding their maintenance programs, as aggressive service can prevent pricey break downs and expand the lifespan of your devices.
Examine customer reviews and testimonials to gauge the integrity and top quality of the solution. A credible repair work solution ought to have a history of completely satisfied customers that can testify to their expertise and efficiency. Take into consideration the costs involved, including components and labor. While affordability is essential, prioritize worth-- guaranteeing that the solution meets your functional demands without jeopardizing quality. By meticulously choosing the appropriate repair work solution, businesses can boost their operational effectiveness and minimize disruptions in production.
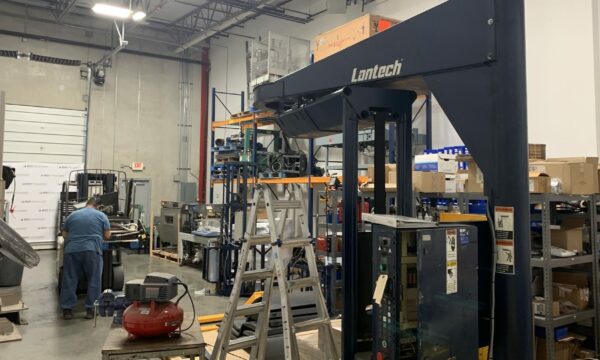
Final Thought
In verdict, timely product packaging device repair service solutions play a crucial function in preserving operational effectiveness. By lessening unplanned downtime, these solutions not just improve manufacturing circulation but additionally contribute to cost financial savings and better devices longevity. Routine maintenance and prompt repair work serve to alleviate minor issues before they intensify, consequently making certain ideal maker efficiency. Eventually, focusing on prompt repairs cultivates a reliable supply view website chain, reinforces staff member spirits, and raises customer contentment via regular product delivery.